
JINGLONG
"Quality pursuit of perfection, credibility to create development"
A professional engaged in electric car plastic parts set research and development, production and sales in one of the integrated enterprise
"Quality pursuit of perfection, credibility to create development"
A professional engaged in electric car plastic parts set research and development, production and sales in one of the integrated enterprise
JINGLONG AUTOMOTIVE INDUSTRY
COOPERATIVE PARTNER
Partners
We work closely with many car companies.
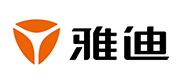
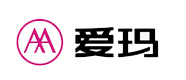
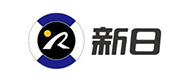
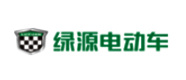
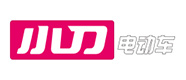
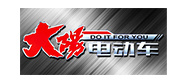
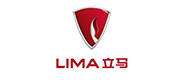
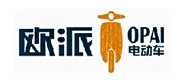
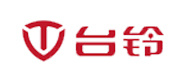
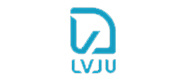
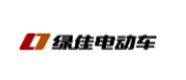
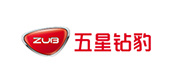
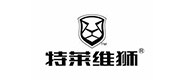
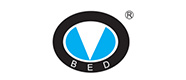
WHY CHOOSE US?
"Quality pursuit of perfection, credibility to create development" is the eternal purpose of the company look forward to your cooperation, create brilliant future!
The company was established in 1998, 26 years of industry experience
Workshop has more than 30 automatic robot injection molding equipment
Each professional electric vehicle manufacturer stable and lasting supporting manufacturers
ABOUT JINGLONG
SINCE 1998
26 Years of Wind and Rain Journey Creates Jinglong Brand Tail Box
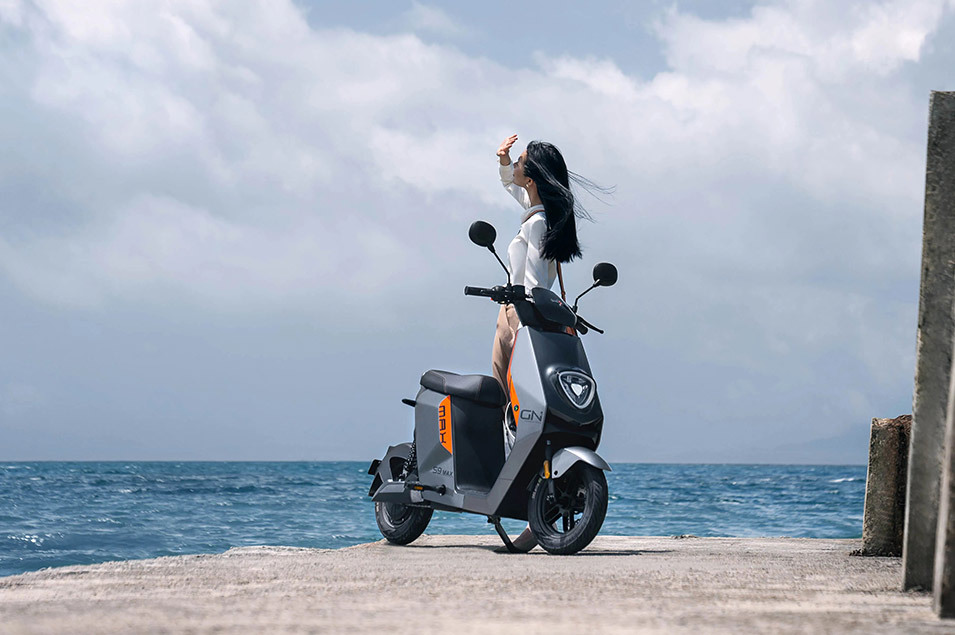
Zhejiang Jinglong Car Industry Co., Ltd.
Zhejiang Jinglong Car Industry Co., Ltd. was founded in 1998 and is now located in Huangyan, the hometown of moulds in China. Is a professional engaged in motorcycle, electric car plastic parts, set research and development, production and sales in one of the integrated enterprise. Since its establishment, with strong technical force and stable talent backing, the company has devoted itself to product research and development and manufacturing with a unique management model, making "Jinglong" brand tail box a leading brand in the motorcycle and electric vehicle plastic parts industry. The industry now has more than 30 modern automated robot injection molding machines and various testing equipment. With stable product quality and efficient production efficiency, it has established a leading position in China's motorcycle and electric vehicle tail box plastic parts industry, and has become a stable and lasting supporting manufacturer for professional motorcycle and electric vehicle manufacturers.
JINGLONG
News Center
Battery car rear trunk abs material and pp material which is more resistant to high temperature?
09-05
The thermal deformation temperature of ABS plastic (acrylonitrile-butadiene-styrene) is 93~118 ℃, and the products can be increased by about 10 ℃ after annealing, the melting temperature is 217~237 ℃, and the thermal decomposition temperature is above 250 ℃.
Is the rear trunk made of PP material strong?
09-05
Good toughness: PP material has a certain degree of toughness, in a certain degree of external impact, such as a slight collision, extrusion, etc., is not easy to break immediately.
What are the precautions for the material of the rear trunk ABS of the battery car
09-05
Avoid high temperature environment: the thermal deformation temperature of ABS plastic is 70 - 107 ℃ (generally around 85 ℃).